Exploding rocks: the UK’s first Selfrag machine
BGS’s new Selfrag machine is helping to unearth the history of rocks.
09/03/2021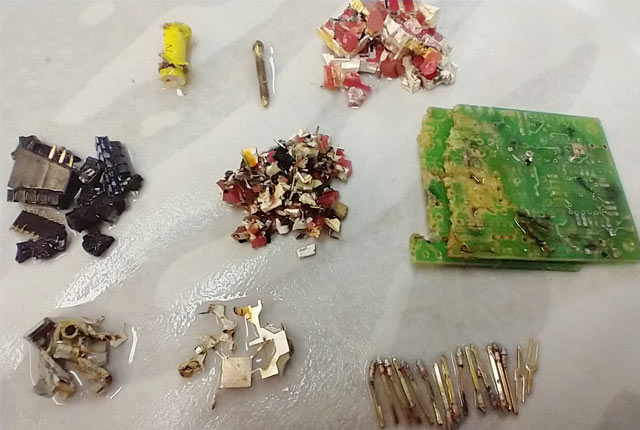
Rocks tell stories. There are chapters about ancient lifeforms, from the microscopic to the very large, chapters about past climate, about the birth of mountain ranges and whole continents, and about the resources that fuel our modern world. To read the chapters, we have to break the rocks down to their constituent elements. This is a rather inefficient process, which involves loud noises, lots of dust, and heavy machinery with moving parts, none of which are particularly good for the health of the scientist involved. More importantly, this is a process that often destroys fragile fossils and minerals. Information is lost and the story gets muddled.
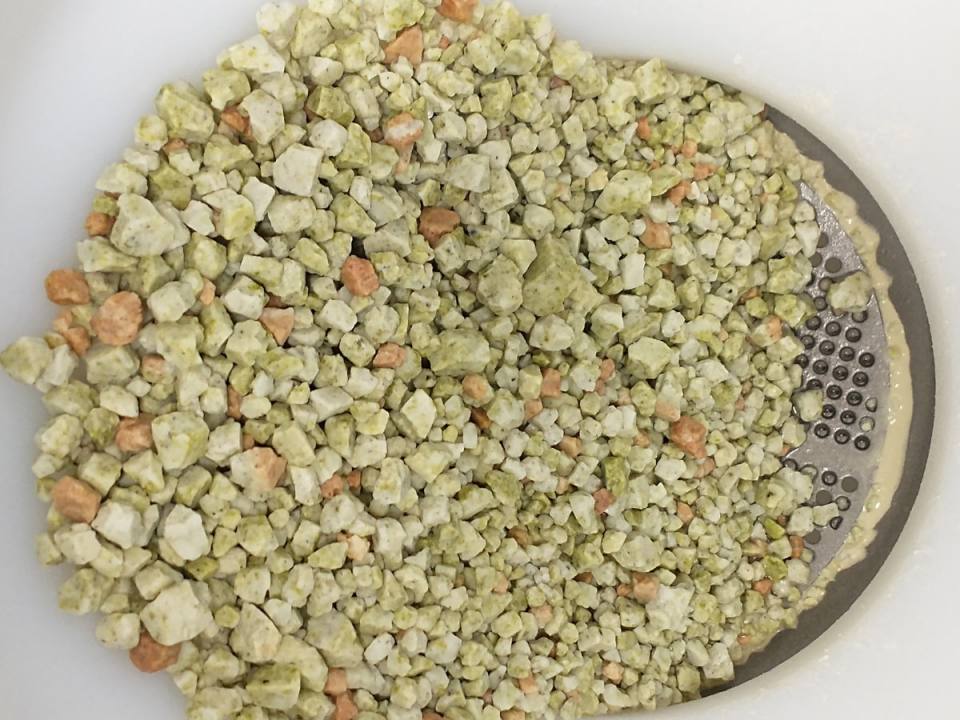
The Selfrag fragments rocks along the boundaries between different types of crystals. The different colours correspond to different minerals. Source: © Diana Sahy / BGS
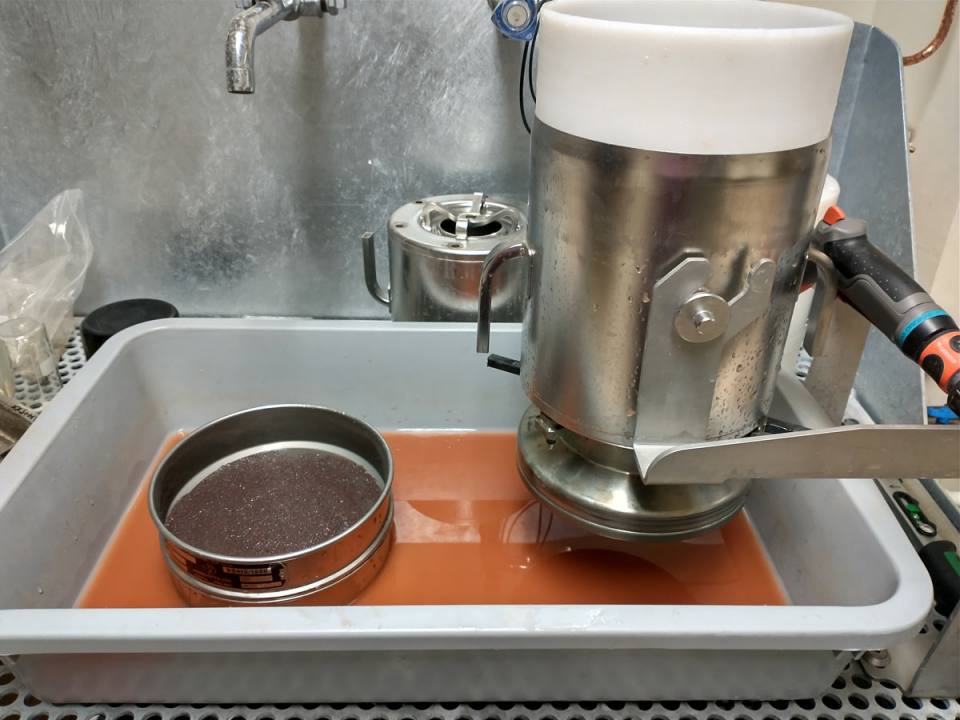
A Jurassic volcanic ash bed from the UK being processed to recover zircon crystals for high-precision U-Pb dating. Source: © Diana Sahy / BGS
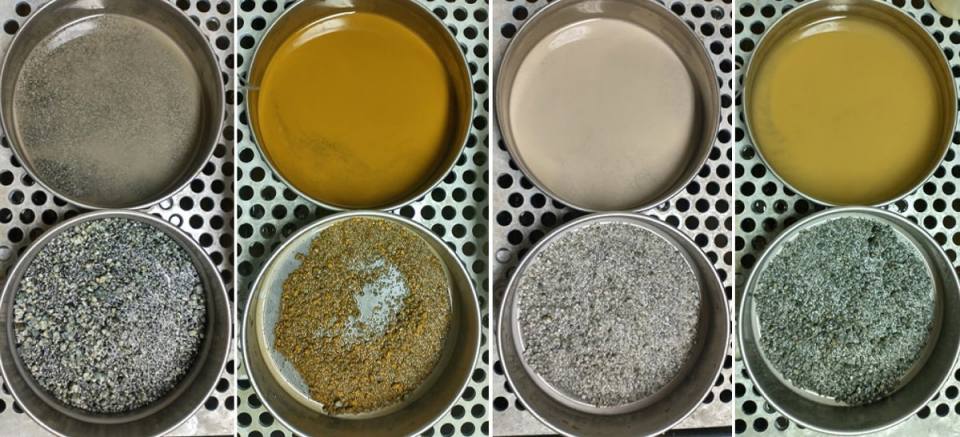
Processing a suite of rocks from the southwest Indian mid-ocean ridge. Differences in colour indicate different rock types and mineralogical compositions. Source: © Diana Sahy / BGS
As is often the case, modern technology comes to the rescue, in the form of a Selfrag (SELective FRAGmentation) instrument recently acquired by BGS with funding from UKRI. Made by Swiss company Selfrag, this is the first such instrument in the UK and one of only 40 around the world so far, with applications ranging from geoscience to ore processing in the mining industry and the recycling of electronic waste.
In the simplest of terms, the Selfrag is a machine that breaks up rocks and other materials using lightning. Granted, it is a small lightning strike, safely contained within a processing chamber and with about a million times less energy than the natural variety, but it is lightning nonetheless. The more scientific explanation is that the rocks are electrodynamically fragmented, which involves discharging up to 200 kV of electricity into the rock, five times per second, which then travels along a path of least resistance, normally the flat surfaces of minerals, causing the rock to selectively fragment along the boundaries between different minerals instead of through minerals, as can happen with mechanical crushing.
As the rock is essentially falling apart rather than being crushed, the process preserves the grainsize distribution of the original rock. This is important because we often want to recover multiple types of minerals and crystals of different sizes from the same rock. For example, we might look at layers of volcanic ash deposited around the time of major extinction event, such as the demise of the dinosaurs, and we might want to determine the age of those layers using multiple methods to ensure that the results are as accurate as possible. This would require us to recover 100 µm zircon crystals, a target mineral for U-Pb dating, and mm-scale feldspar, a target mineral for Ar/Ar dating from the same sample. Or we might want to recover a suite of different minerals of sizes ranging from microns to millimeters to chart the history of metamorphic rocks, the building blocks of mountain ranges. Paleontologists studying ancient ecosystems may want to look at a range of different microfossils of varying sizes, or may wish to recover both juvenile and adult populations of the same species.
To achieve these goals through crushing and milling, we would need to process several pieces of each sample separately, because milling rocks to a fine enough powder to liberate the tiniest crystals would destroy larger grains. With the Selfrag, the same result can be achieved using a single piece of rock in a fraction of the time required by conventional methods. Because samples are processed in an enclosed vessel, the chances of sample loss or contamination are reduced, which allows us to use smaller samples while eliminating most of the noise- and dust-related health and safety concerns associated with traditional rock processing.
Aside from the really cool science, the Selfrag has real-world applications as well. These applications are tied to the never-ending need for resources to fuel our modern lifestyles, and the requirement to improve our capacity to reuse and repurpose the resources we already have, to ensure said lifestyle becomes sustainable. Our laboratory-sized machine is being used to conduct experiments on the efficient fragmentation of metallic and non-metallic ores. The technology can then be scaled up to machines that can fragment many tonnes of rock per day improving the energy efficiency of ore processing in the mining industry. The recycling industry is another promising area of research and development where the goal is to become more efficient at recycling consumer electronics, which can be fragmented to separate out glass, plastic and metal components, as well as the recovery of metals from the ash produced by energy from waste incinerator plants.
The Selfrag machine at the British Geological Survey is a relatively ‘young’ instrument, having been commissioned in September 2020, and we are in the process of building up a network of UK partners across the geosciences and beyond, with the aim of helping the academic and industry community acquire better data on a wide range of materials. I look forward to developing this facility over the coming years, and exploring the limits of this technology to help read the stories of our past and write the stories of our future.
The Selfrag capability at BGS is part of the National Environmental Isotope Facility was made possible through NERC funding.
About the author
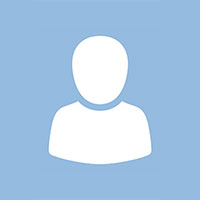
Dr Diana Sahy
Isotope research scientist
Diana Sahy is a geochronologist at the British Geological Survey, specialising in determining the age of rocks based on the radioactive decay of uranium. Diana leads the newly established Selfrag facility, as well as BGS’ uranium-thorium geochronology laboratory, where her main research focus is the timing, causes and environmental impact of seafloor methane emissions on a regional scale.
Find out moreRelative topics
Related news
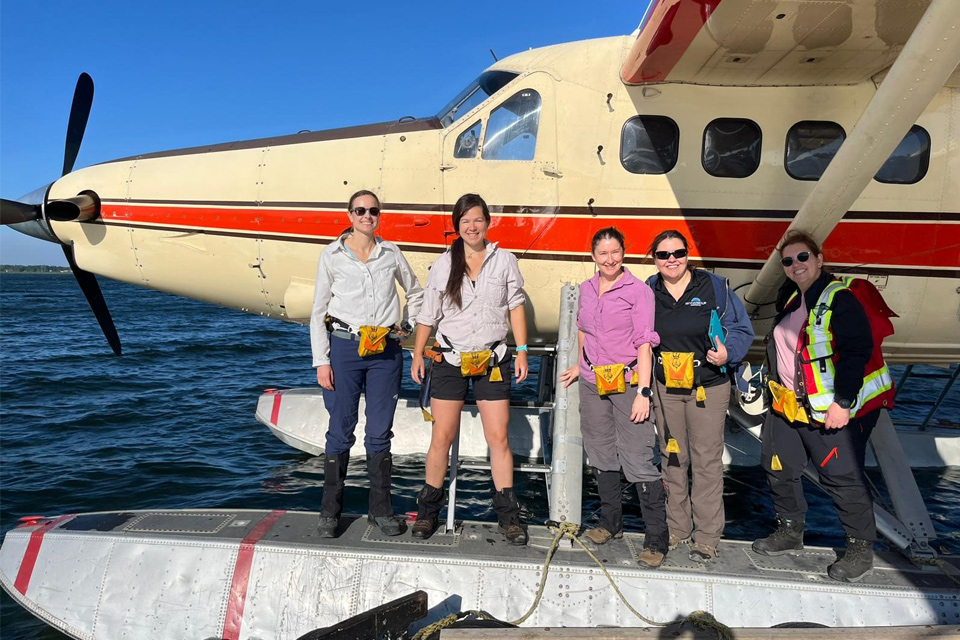
Funding awarded to UK/Canadian critical mineral research projects
08/07/2025
BGS is part of a groundbreaking science partnership aiming to improve critical minerals mining and supply chains.
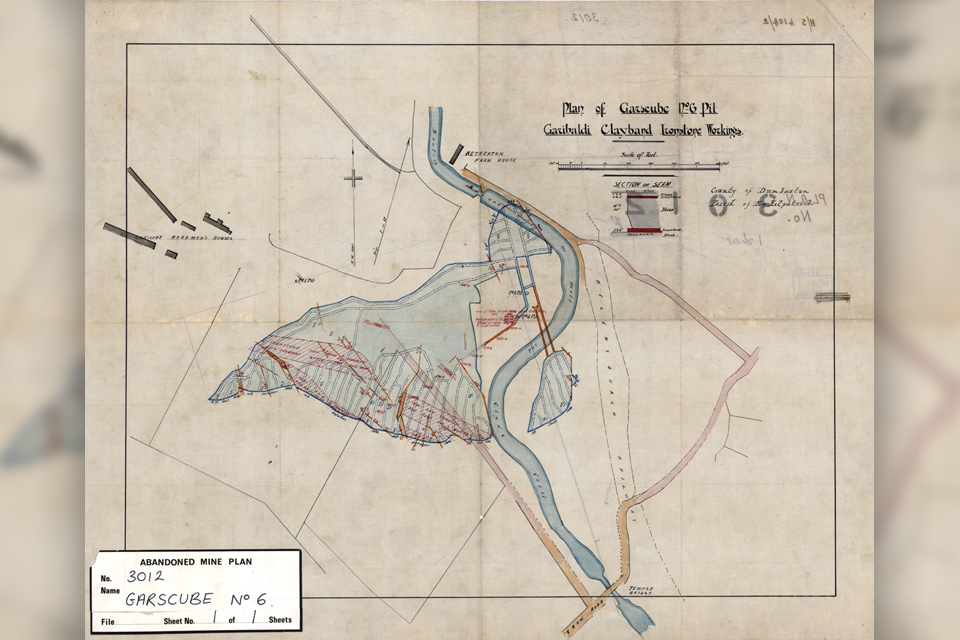
Release of over 500 Scottish abandoned-mine plans
24/06/2025
The historical plans cover non-coal mines that were abandoned pre-1980 and are available through BGS’s plans viewer.
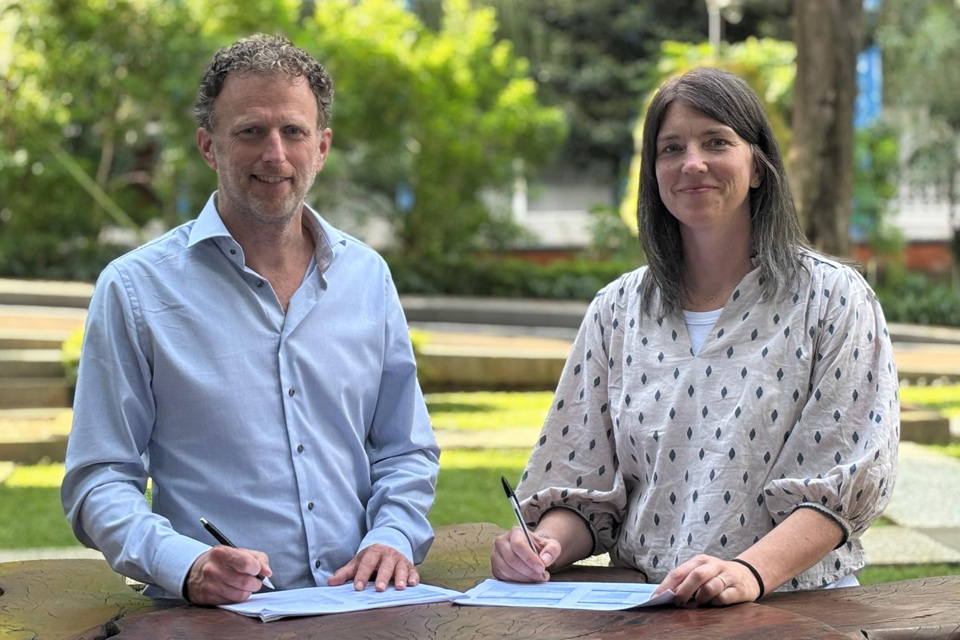
New collaboration aims to improve availability of real-time hazard impact data
19/06/2025
BGS has signed a memorandum of understanding with FloodTags to collaborate on the use of large language models to improve real-time monitoring of geological hazards and their impacts.
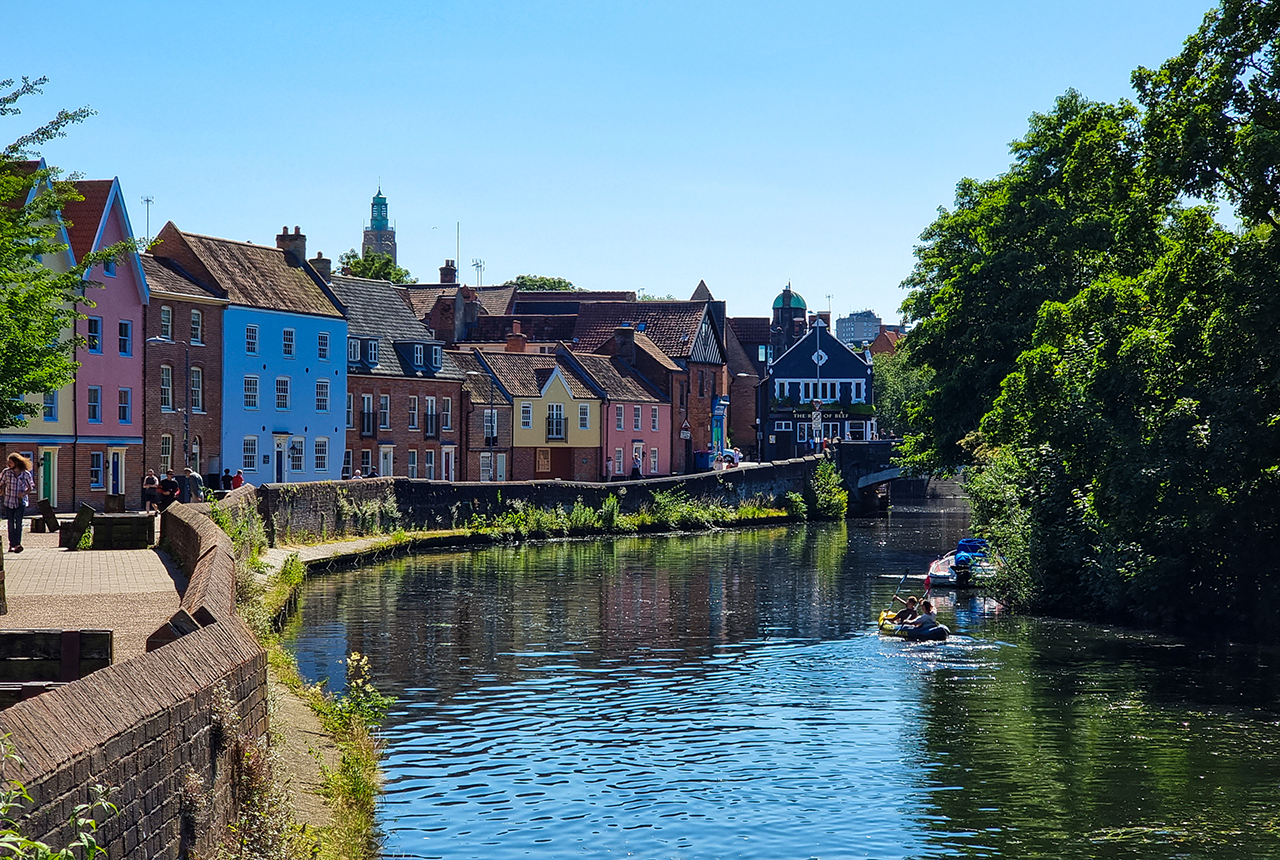
Modern pesticides found in UK rivers could pose risk to aquatic life
17/06/2025
New research shows that modern pesticides used in agriculture and veterinary medicines have been found for the first time in English rivers.
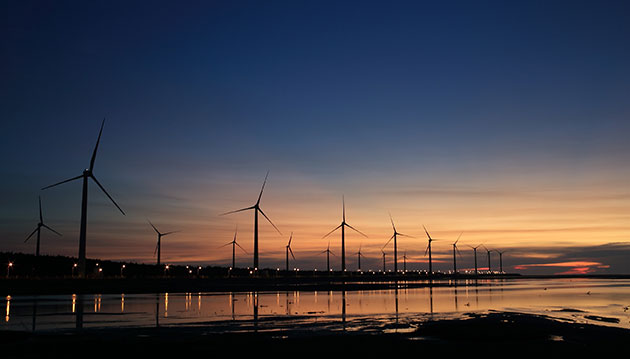
Goldilocks zones: ‘geological super regions’ set to drive annual £40 billion investment in jobs and economic growth
10/06/2025
Eight UK regions identified as ‘just right’ in terms of geological conditions to drive the country’s net zero energy ambitions.
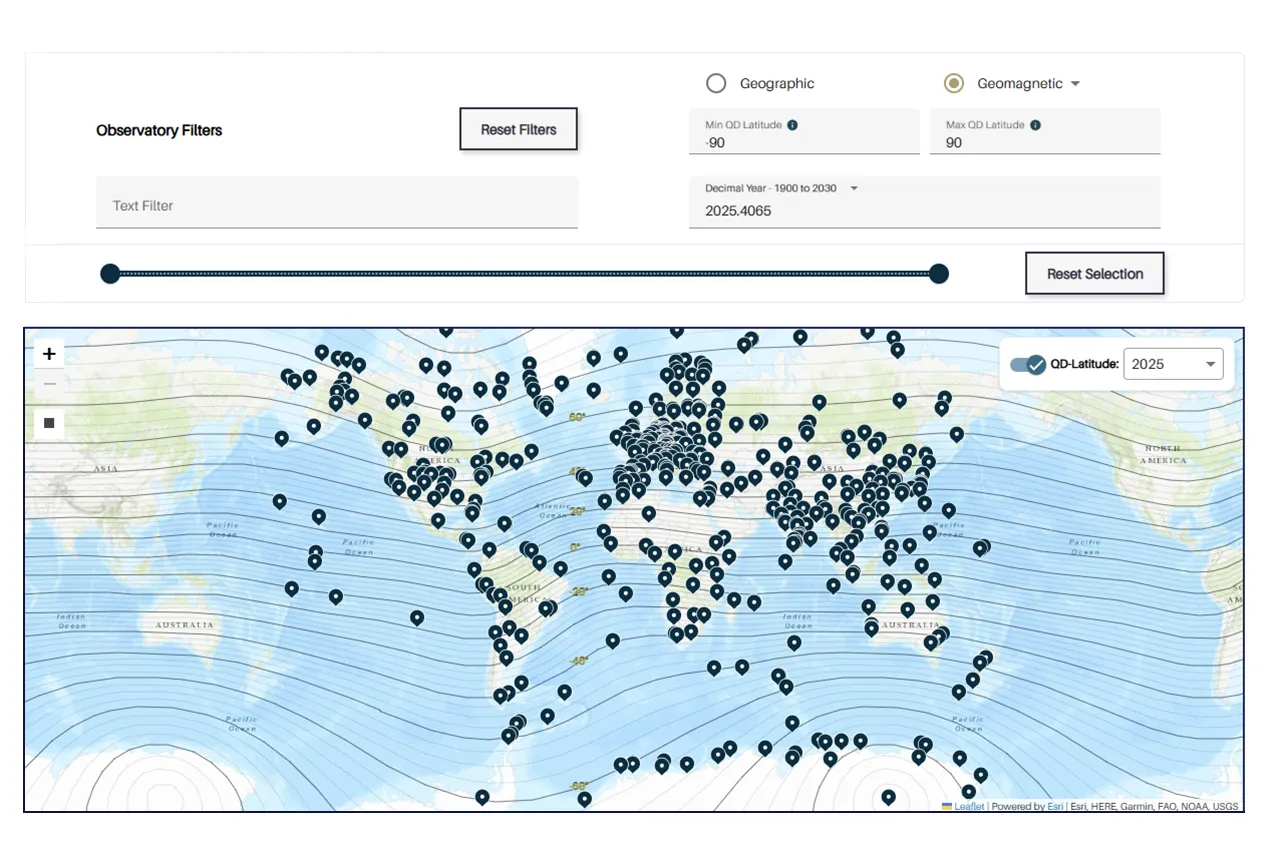
Upgraded web portal improves access to geomagnetism data
02/06/2025
BGS’s geomagnetism portal, which holds data for over 570 observatories across the world, has received a significant update.
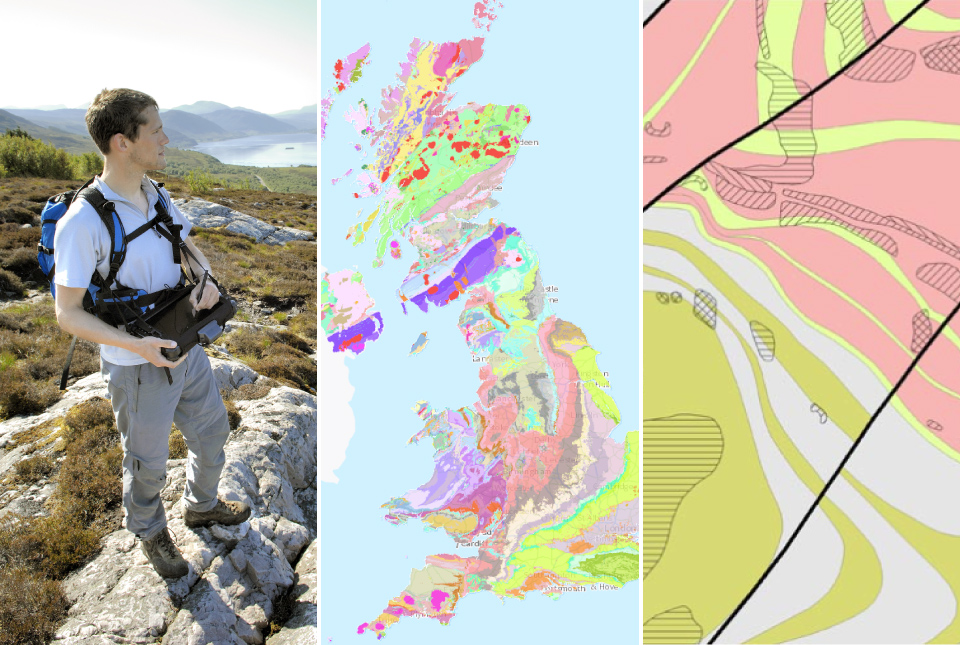
BGS digital geology maps: we want your feedback
29/05/2025
BGS is asking for user feedback on its digital geological map datasets to improve data content and delivery.
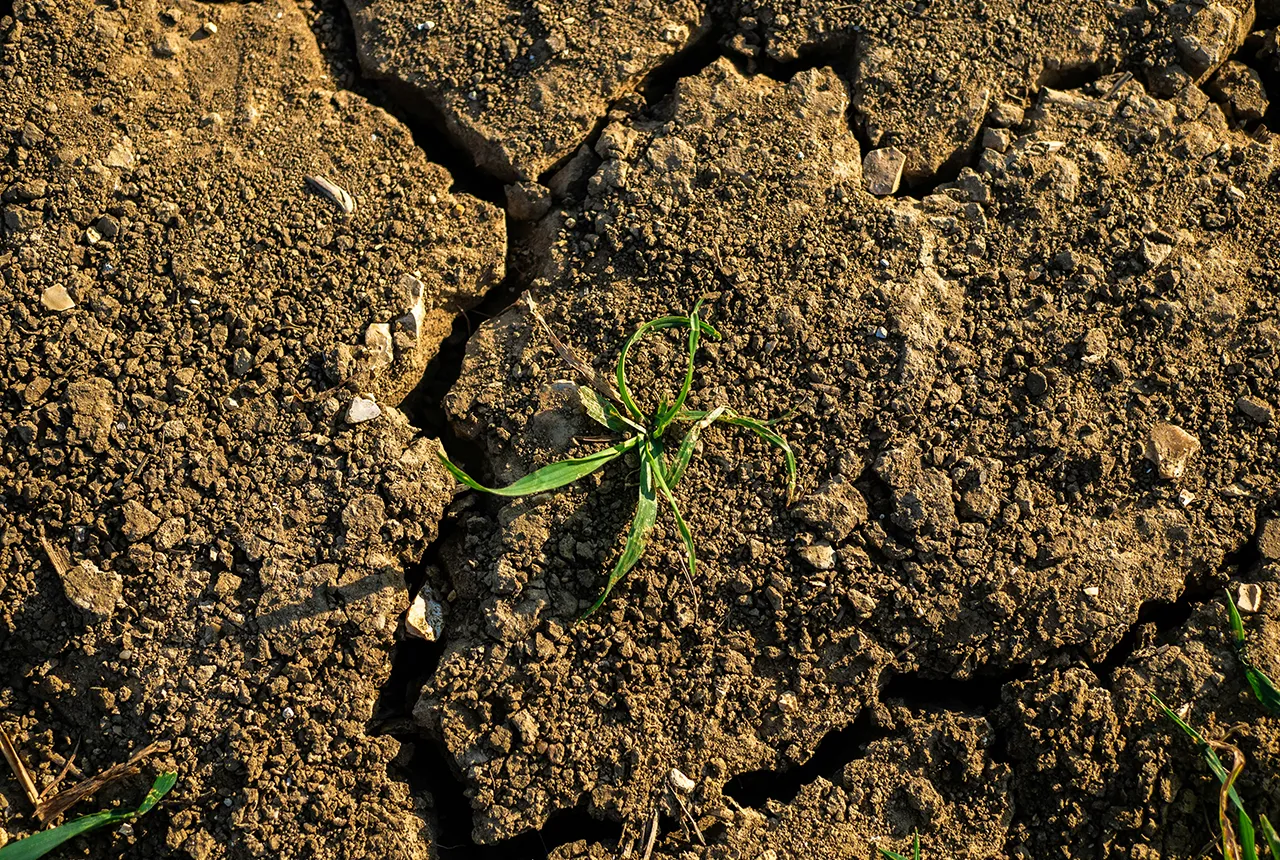
What is the impact of drought on temperate soils?
22/05/2025
A new BGS review pulls together key information on the impact of drought on temperate soils and the further research needed to fully understand it.
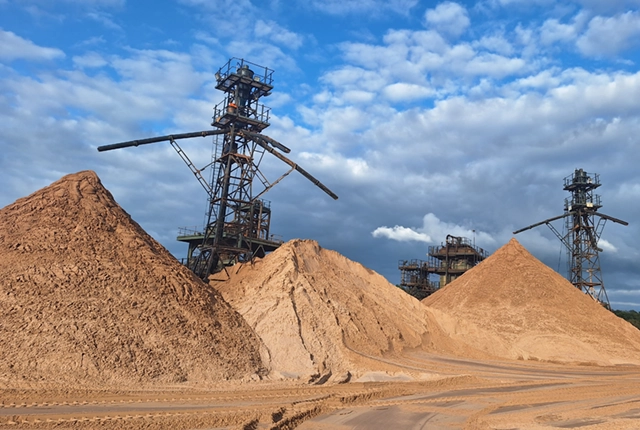
UK Minerals Yearbook 2024 released
21/05/2025
The annual publication provides essential information about the production, consumption and trade of UK minerals up to 2024.
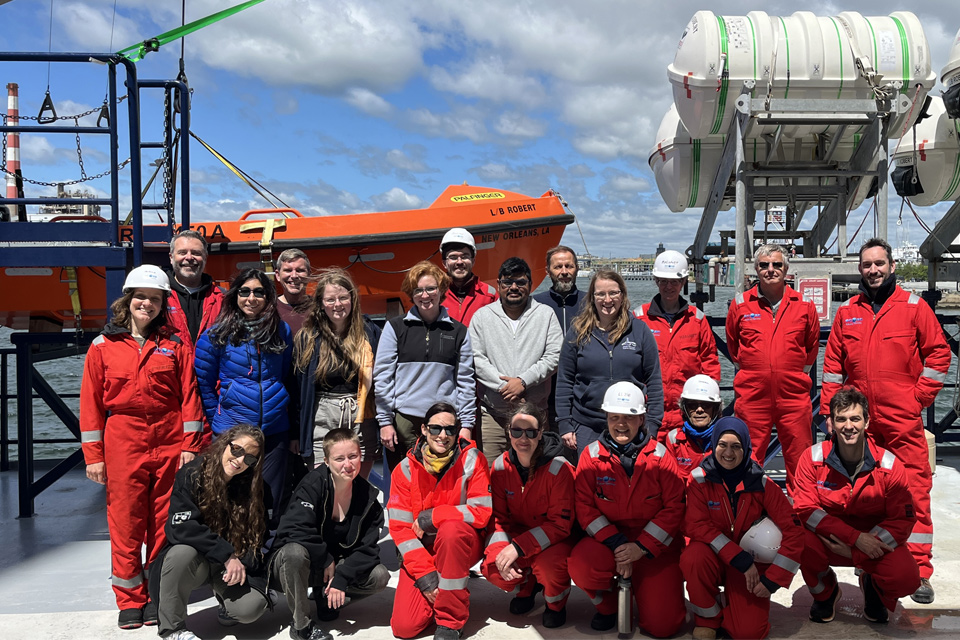
BGS scientists join international expedition off the coast of New England
20/05/2025
Latest IODP research project investigates freshened water under the ocean floor.
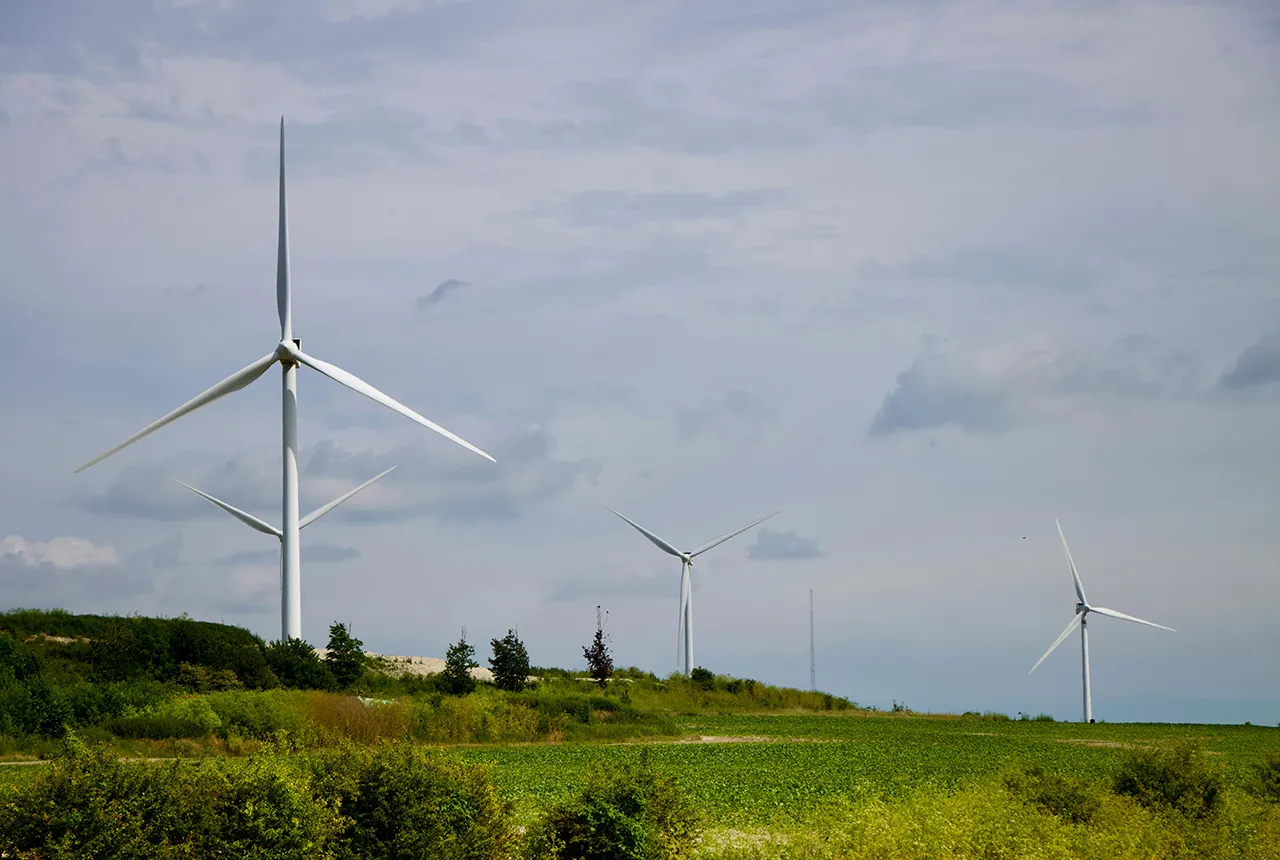
New interactive map viewer reveals growing capacity and rare earth element content of UK wind farms
16/05/2025
BGS’s new tool highlights the development of wind energy installations over time, along with their magnet and rare earth content.
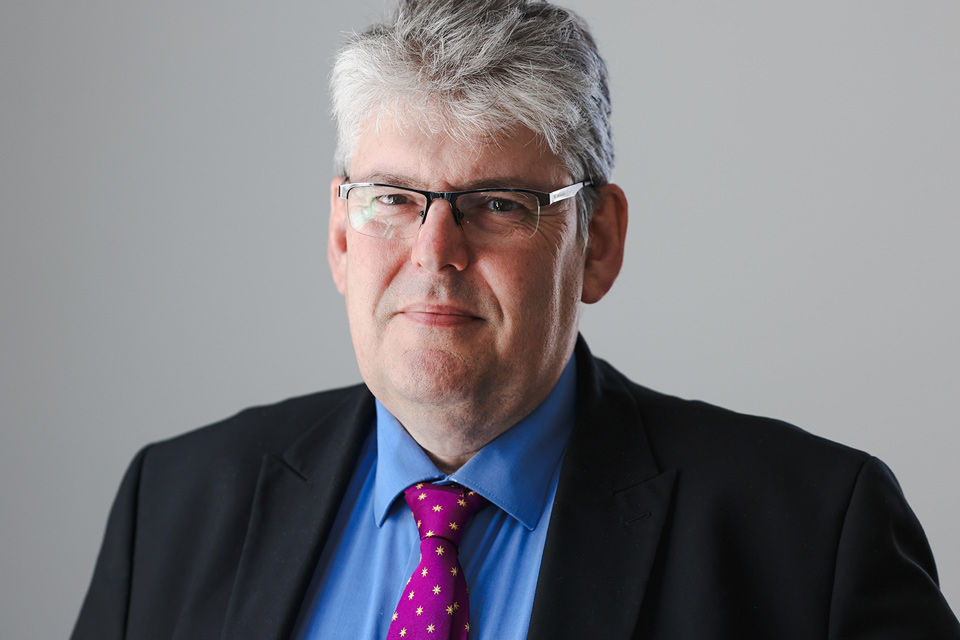
UKRI announce new Chair of the BGS Board
01/05/2025
Prof Paul Monks CB will step into the role later this year.